Os operadores de caldeiras e fornos estão sempre procurando maneiras de aumentar o desempenho da combustão. Um otimizador de combustão projetado para melhorar a eficiência e reduzir as emissões pode ajudar.
Ele suporta uma operação mais flexível em caldeiras e fornos, manipulando as configurações de controle de combustível e ar por meio de polarizações de circuito fechado. Isso melhora as características de combustão permitindo operar na zona ideal da mistura do combustível mais o ar, melhorando a taxa de calor, evitando altas emissões poluentes de CO e NOx.
O endurecimento contínuo das regulamentações ambientais e o aumento dos preços dos combustíveis tem sacrificado a economia da planta. A única opção para as instalações que podem permanecer abertas é encontrar maneiras de aumentar a eficiência do sistema da combustão. Isso inclui a introdução de tecnologia para reduzir custos, minimizar emissões, economizar combustível e melhorar a lucratividade.
Mas os desafios operacionais são frequentemente levantados ao fazer grandes mudanças que não faziam parte do projeto original.
Combustíveis diferentes, falhas constante de operação, instalações de equipamentos de controle não efetivos, variação de carga para permitir que as energias renováveis operem na rede e adicionar a capacidade de acelerar mais rapidamente são exemplos de algumas das abordagens adotadas pelos operadores para melhorar a equação de custo. No entanto, é provável que essas mudanças coloquem grande pressão nos setores de operações e manutenção das indústrias.
Zona de conforto não lucrativa
Torna-se essencial, portanto, otimizar os processos para reduzir as emissões poluentes, aumentar a eficiência de caldeiras e fornos, minimizar os custos com combustíveis e com a manutenção e melhorar o desempenho e a disponibilidade da unidade. A chave para alcançar isso no mercado atual é operar estes sistemas de aquecimento no ponto operacional mais lucrativo.
Falhas constantes
É difícil para a equipe de operações monitorar e ajustar continuamente os parâmetros da mistura do combustível e ar na tentativa de responder às mudanças na carga da unidade, nas características do combustível e na dinâmica da caldeira ou do forno sem prévio conhecimento de combustão e de equipamentos de controle para correta aplicação a estas máquinas.
Designar alguém em tempo integral para micro gerenciar os processos da combustão sem este conhecimento, sem treinamento e interação mais profunda do processo é perda de tempo e dinheiro, a prática mais usual hoje encontrada na indústria é a “zona de conforto”. A indústria perde milhões quando se estabiliza nesta ‘’zona de conforto’’ nos sistemas de aquecimento industrial.
A zona de conforto é uma faixa operacional onde os operadores creem que o sistema de combustão da máquina, está no ponto correto e completo sendo muitas vezes utilizados ajustes com ajuda de manutenção corretiva.
Operar nesta zona de conforto ajuda as plantas a aumentar o potencial de combustão incompleta destas máquinas. No entanto, possui um efeito prejudicial imediato, acumulativo em médio e a longo prazo. Com o tempo, a operação dentro da zona de conforto diminui a eficiência geral da máquina, aumenta as emissões poluentes, aumenta os custos com consume de combustíveis pela não completa combustão e reduz a lucratividade.
O motivo
Essa zona de conforto geralmente fica em um ponto em que o risco de altas emissões de monóxido de carbono (CO) não são analisadas ou corrigidas. Ao manter uma margem segura de um pico de emissões de CO, as plantas são forçadas a operar com níveis mais altos de O2 e NOx . Essa abordagem de ‘’zona de conforto’’ é impraticável funcionar desta maneira nas industrias, exigências ambientais mais rigorosas e as perdas com combustíveis a tornam um jogo onde não há retorno. Perder a conformidade mesmo por períodos curtos pode eliminar a pouca lucratividade que possa existir.
A zona de conforto utilizada por muitas indústrias prejudica a lucratividade.
Existe uma zona ótima de operação, mas requer um melhor controle dos processos da combustão. Dentro da zona de conforto existe a queda da eficiência na combustão, aumento do excesso de ar, aumento do NO x, diminuição proporcional do CO, ou seja, a queima incompleta do combustível, o que caracteriza uma zona não ideal de operação. Os ajustes manuais não são capazes de permanecer no intervalo da Zona Eficiente consistentemente por um longo período de tempo.
A única forma de alcançar este objetivo é através da otimização das condições da combustão destas maquinas via análise dos gases da combustão, buscando o real equilíbrio entre a mistura do combustível mais o ar.
Equilíbrio de Material e Energia.
O controle da combustão requer um fluxo de ar compatível com o fluxo de combustível. A quantidade de ar necessária para queimar uma unidade de massa de combustível depende principalmente no teor de água e do poder calorífico do combustível.
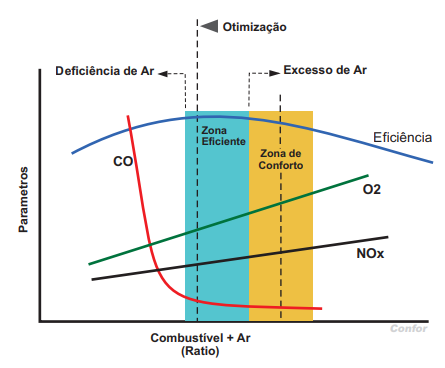
A zona de conforto utilizada por muitas indústrias prejudica a lucratividade.
Existe uma zona ótima de operação, mas requer um melhor controle dos processos da combustão. Dentro da zona de conforto existe a queda da eficiência na combustão, aumento do excesso de ar, aumento do NO x, diminuição proporcional do CO, ou seja, a queima incompleta do combustível, o que caracteriza uma zona não ideal de operação. Os ajustes manuais não são capazes de permanecer no intervalo da Zona Eficiente consistentemente por um longo período de tempo. A única forma de alcançar este objetivo é através da otimização das condições da combustão destas maquinas via análise dos gases da combustão, buscando o real equilíbrio entre a mistura do combustível mais o ar.
Equilíbrio de Material e Energia.
O controle da combustão requer um fluxo de ar compatível com o fluxo de combustível. A quantidade de ar necessária para queimar uma unidade de massa de combustível depende principalmente no teor de água e do poder calorífico do combustível. Portanto, mesmo que o comportamento da combustão seja representado por outros cenários, a prevenção de excesso de combustão incompleta usando a resposta de um analisador de gases pode ser referido como controle de bloqueio de anormalidade de gás CO:
- Quando o queimador é aceso e há uma mudança temporária no equilíbrio entre a quantidade de combustível e ar na combustão
- Quando o controle automático é implementado para a quantidade de combustível e ar como resultado de uma mudança no poder calorífico do combustível, e há uma mudança temporária na relação de excesso de ar, independentemente de não haver flutuação na carga de vapor da caldeira ou massa de calor em um forno.
- Quando a quantidade de ar e combustível é controlada via controle de ar rico (ar excessivo) para evitar a ocorrência de fumaça preta, e há uma mudança temporária de direção que torna a redução da taxa de excesso de ar em momentos de aumento repentino na carga da caldeira ou do forno.
Otimização da Combustão
Os analisadores de gases de combustão foram projetados para monitorar e melhorar a eficiência de combustão e reduzir as emissões poluentes em processos de combustão. Sistemas fixos podem ser instalados em fornos e caldeiras. Ao mesmo tempo, suporta uma operação mais flexível, manipulando as configurações de controle de combustível e ar por meio de polarizações de circuito fechado. Isso melhora as características da combustão permitindo operar na zona ideal sem derivar para a zona de altas emissões de CO ou NOx.
A instalação de Analisadores de gases da combustão, não requer modificações da máquina de aquecimento. Ele monitora os dados do processo automaticamente para determinar tendências ideais para as variáveis a serem manipuladas. Transmite os dados a um sistema de controle IHM ou PLC, informando os níveis de O2, CO, CO2, ou outros gases da combustão para serem corrigidos no processo, podendo acionar sistemas da malha de controle do sistema destas máquinas para os melhores níveis de eficiência. As informações podem ser utilizadas para ajustes de queimadores, controle de entrada de ar
primário ou secundário da combustão, etc.
Os resultados de otimização
Muitos benefícios da implementação da otimização da combustão são de reduzir o alto consumo de combustíveis e um maior controle das emissões poluentes e outros dados como:
- Controle do excesso de ar na combustão,
- Controle das pressões diferenciais,
- Controle de Temperaturas de saída do ar primário e secundário,
- Controle de cargas de combustíveis,
- Controle do CO na combustão,
- Controle da taxa de calor,
- Controle de emissões e opacidade dos gases,
- Melhor interação do operador com os sistema de controle da combustão,
- Ajustes de alarmes de falhas de dados em sistemas de IHM,
- Diminuição progressiva de reparos e manutenção da máquina,
- Recuperação e aumento das Cotas de CO, etc.
O custo benefício
O retorno é bastante rápido em relação as perdas com combustíveis não queimados e má regulagem da combustão, manutenção excessiva da máquina, etc. Naturalmente este retorno está condicionado ás limitações de engenharia da caldeira ou do forno. A recuperação e os balanços de energia são necessários para avaliação do desempenho destas máquinas após implantação da otimização.
Evidentemente com um melhor controle do sistema de combustão o potencial energético da indústria aumenta. As perdas da recuperação dos combustíveis no processo, aparecem quando os gastos forem contabilizados, quando se determinar uma eficiência maior destas máquinas.
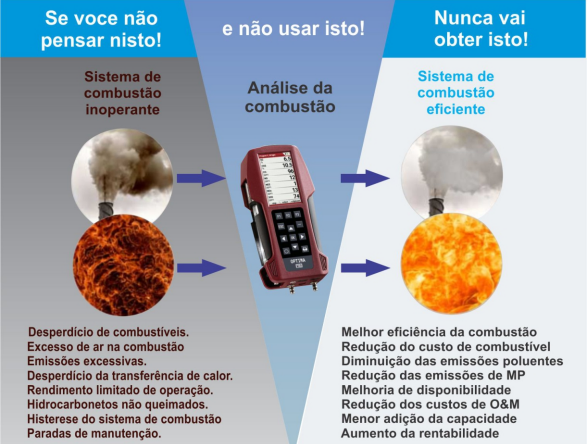
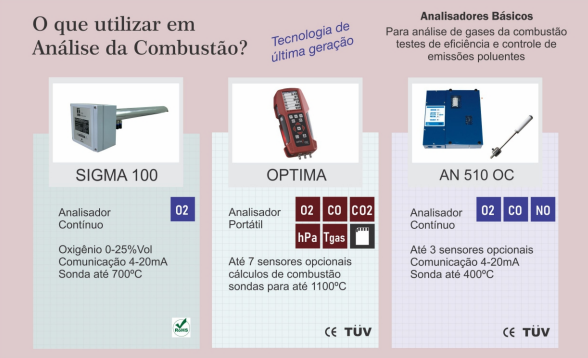